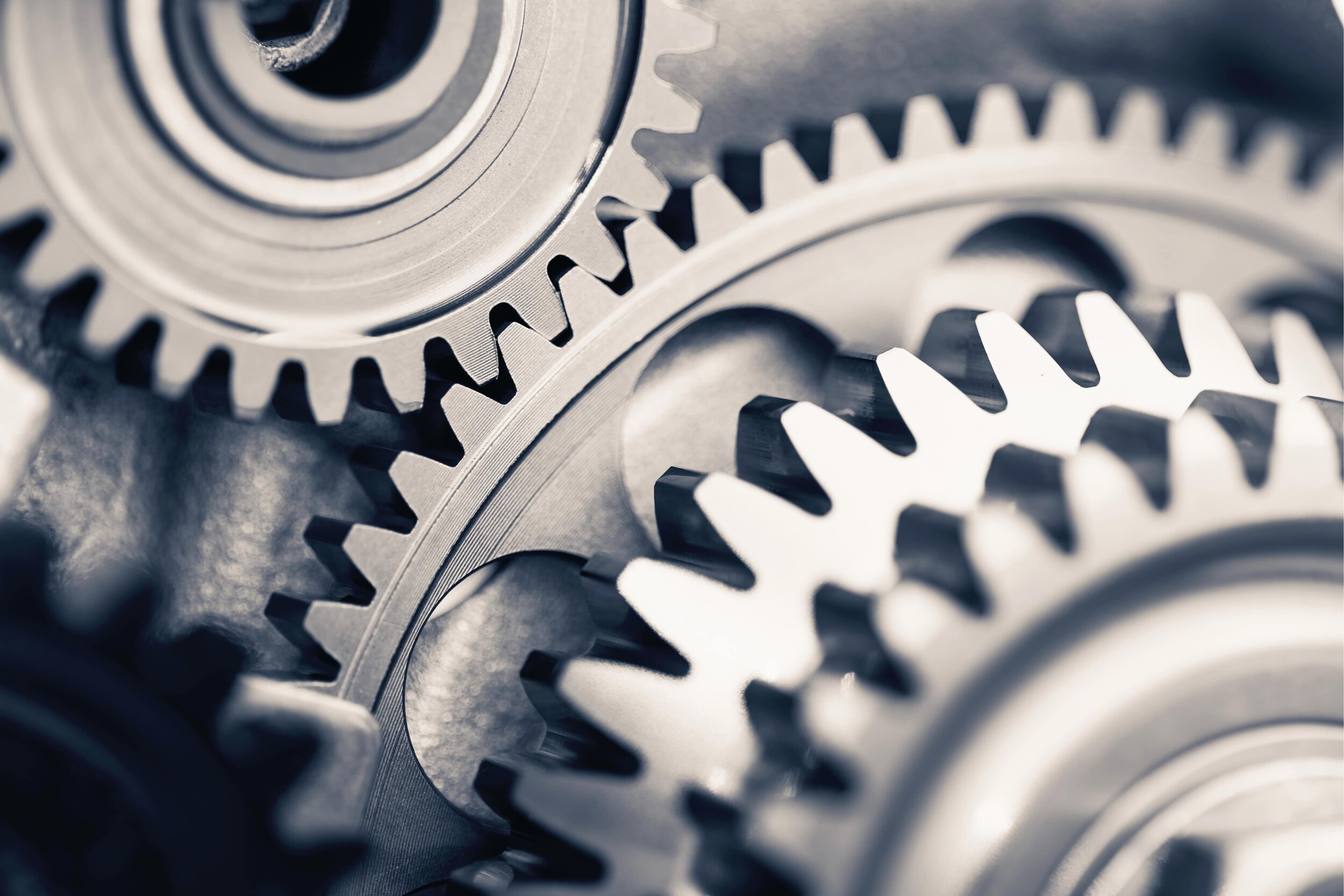
RMW Blog
Precision Machining
Automate & Innovate: Robotic Welding Insights
In the ever-evolving landscape of manufacturing and fabrication, robotic welding stands as a testament to innovation and efficiency. Harnessing the precision and reliability of automation, robotic welding offers a plethora of advantages…
Automate & Innovate: Robotic Welding Insights
In the ever-evolving landscape of manufacturing and fabrication, robotic welding stands as a testament to innovation and efficiency. Harnessing the precision and reliability of automation, robotic welding offers a plethora of advantages while presenting a few challenges to navigate. Let's delve into the realm of robotic welding, exploring its benefits, drawbacks, and the driving force behind its relentless pursuit of quality improvement and efficiency gains.
Advantages:
Precision and Consistency: Robotic welding systems are programmed to execute welds with unparalleled precision, ensuring consistent quality across every project. This precision minimizes errors and produces uniform welds, enhancing overall product integrity.
Increased Productivity: By automating the welding process, robotic systems can operate continuously without the need for breaks, resulting in significantly higher productivity compared to manual welding. This increased throughput accelerates project timelines and boosts overall efficiency.
Cost Efficiency: While the initial investment in robotic welding technology may be substantial, the long-term cost savings are undeniable. Reduced labor costs, decreased material waste, and higher productivity contribute to a lower cost per part and improved profitability over time.
Disadvantages:
Initial Investment: Implementing robotic welding systems requires a considerable upfront investment in equipment, programming, and training. Smaller businesses may find the initial cost prohibitive, limiting access to this technology.
Flexibility Limitations: While robotic welding excels in repetitive, high-volume production environments, it may lack the flexibility required for custom or low-volume projects. Adapting robotic systems to accommodate varying part geometries or welding processes can be challenging and time-consuming.
Reasons for Quality Improvement and Efficiency Gains:
Continuous Innovation: As technology advances, robotic welding systems incorporate new features and capabilities to enhance precision, speed, and reliability. Continuous investment in research and development drives quality improvement and efficiency gains across the industry.
Integration of Advanced Sensors: Robotic welding systems increasingly utilize advanced sensors and feedback mechanisms to monitor weld quality in real-time. This proactive approach allows for immediate adjustments to optimize weld parameters and ensure superior quality.
Emphasis on Training and Education: Training programs and certifications for robotic welding operators and technicians play a crucial role in maintaining quality standards and maximizing efficiency. Well-trained personnel can effectively program, operate, and troubleshoot robotic systems, minimizing errors and maximizing productivity.
In conclusion, robotic welding offers a myriad of advantages, including precision, productivity, and cost efficiency, while presenting challenges such as initial investment and flexibility limitations. However, with a commitment to continuous improvement, integration of advanced technologies, and investment in training and education, the future of robotic welding holds limitless potential for quality enhancement and efficiency gains in the fabrication industry.